A device to make it easier for veterinarians to extract the objects our pets swallow. . .
A state-of-the-art ‘surround sound’ studio where audio and music engineering students can immerse listeners in their sonic creations . . .
A better way for heart surgeons to repair or replace faulty mitral valves . . .
A 70-foot tall “periscope” so residents of New Rochelle can view the ocean from the town square . . .
These are among more than 80 projects that seniors in five engineering departments and computer science—as well as students in the Medical Technology & Innovation Masters Degree Program—will showcase with posters and prototypes on May 5 at the annual Design Day of the Hajim School of Engineering and Applied Sciences.
The event will be held in the Goergen Athletic Center on the River Campus from 10:30 a.m. to 1:30 p.m.
THE QUADCAST PODCAST: Design Day 2017
Senior students in the engineering departments complete a capstone project in accordance with requirements of the Engineering Accreditation Commission of ABET, which accredits college and university engineering schools and departments worldwide.
“Design Day presents a wonderful opportunity for students to showcase their efforts to translate their engineering knowledge into practice,” says Wendi Heinzelman, dean of the Hajim School. “It is always exciting to see the wide range of projects and to speak with the students to understand the thought process — and the hard work — that went into the final designs.
“Creating a product that satisfies a real need while meeting practical design constraints is challenging, but succeeding in this endeavor is rewarding and can provide significant benefit to the intended customer.”
Design Day gives students a chance to hone their communications skills as they explain their projects to visitors.
Learning by being there: In the operating room
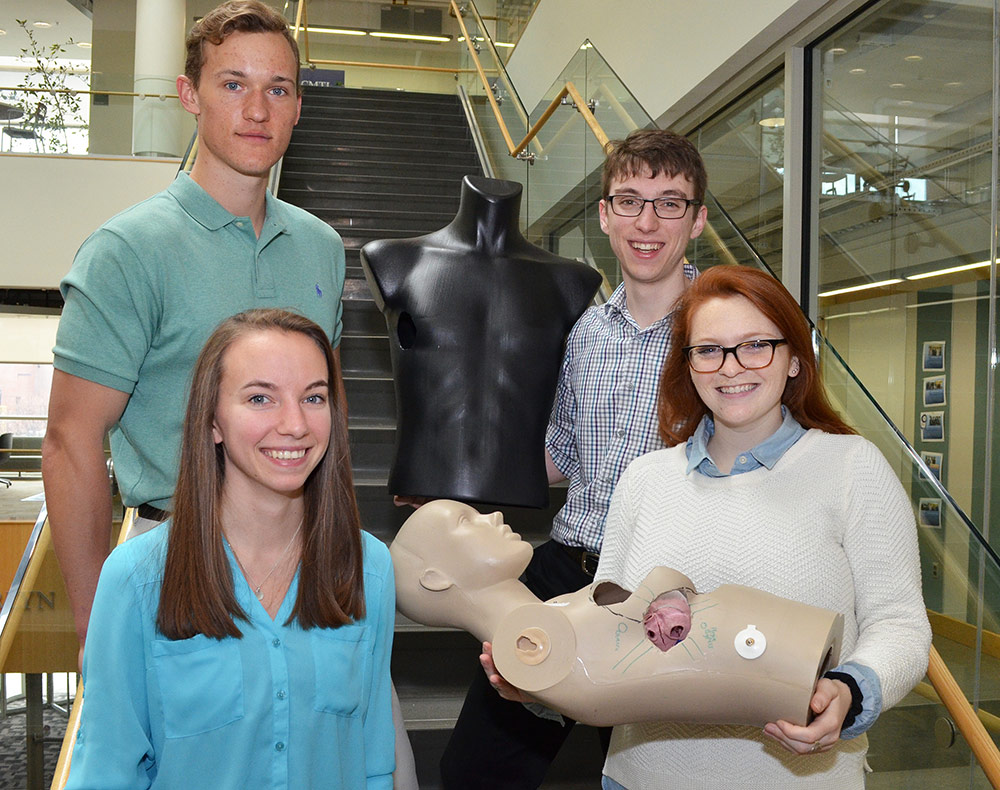
Last summer, Ian Baranowski, Margaret Ferrari, Kyle Meyers, and Lauren Seitz spent eight weeks in operating rooms and diagnostic labs at the University of Rochester Medical Center, witnessing 25 to 30 different kinds of procedures ranging from heart valve surgeries to less invasive angioplasties.
“One day we’d switch from seeing open chest surgeries to going to fluoroscopy labs, and having to put on lead vests so we wouldn’t absorb the radiation when they were trying to image a balloon going through a patient,” Baranowki says.
Immersion in clinical settings is a hallmark of Rochester’s Center for Medical and Technology Innovation master’s program in device design. Thanks to the close proximity of the University’s Medical Center to the River Campus, it is a unique opportunity for budding engineers to learn firsthand—from surgeons, nurses and other clinical staff—what could be done to improve medical tools and processes.
Not only that, the students also get a clearer understanding of how the actual constraints of an operating room or lab must be factored into the solutions they devise.
Baranowski, Ferrari, Meyers, and Seitz—who are refining a device for use in mitral valve replacement surgery—are one of three teams of CMTI students finishing their design projects this spring. The projects are a culmination of a year of rigorous design, market analysis, and instruction in Food and Drug Administration approval processes and intellectual property law.
But all of them started with clinical immersion.
Becoming part of a ‘well-oiled machine’
For Baranowski, Ferrari, Meyers, and Seitz—the cardiovascular team—this sometimes meant standing a mere two or three feet away from a patient undergoing open heart surgery.
“The first day we felt a little out place,” Meyers says, “not knowing where to stand, what to avoid touching, and above all wanting to be respectful to the patients and the process that was going on.”
“At the beginning we were standing at the edges of the room, next to the walls,” Seitz adds.
But the students quickly gained the trust of the operating room nurses, and learned to fit into the “well-oiled machine” of an operating room. They learned the opportune times during open-heart surgery to talk to the perfusionist operating the heart-lung machine, for example, or to ask questions of the industry representative guiding a surgeon in the use of a new device.
“The surgeons would often redirect the camera so we could see what they were looking at,” Baranowski says.
“It’s really beneficial to be doing this at a teaching hospital that already has surgeons committed to teaching students and helping out on projects that advance medicine,” adds Ferrari. The students worked particularly closely with Peter Knight, the Marjorie B. Morris Endowed Professor in Cardiac Surgery, and Fabio Sagebin, a cardiothoracic surgery resident. “They were always willing to meet with us,” Ferrari says.
Knight says he’s “enthusiastic about working with the students as they provide an opportunity to get a fresh, unbiased look at what we do. Our specialty is in need of novel solutions to old problems. “
Narrowing the possibilities
Each day the students kept a log of the procedures they witnessed and a list of the “pain points” associated with each.
During the fall semester they began whittling down a list of 150 to 200 possible projects, by researching the market, examining existing patents, and “trying to figure out where there was an opportunity for us to get our hands dirty,” Meyers says.
“It’s a tricky process. Because the FDA is involved in regulating medical devices, you want to be able to tell them your device is similar enough to what’s already on the market, so you don’t need a lot of testing. But it has to be different enough to merit a patent.”
By October, team members had narrowed the list to six possibilities, which were reviewed during a two-hour presentation in front of a group of investors, CEOs from device companies, and staff from UR Ventures, the University’s technology transfer office.
After hearing their feedback, the team was ready to embark on the project that is now nearing fruition.
A less invasive ‘fix’
Mitral regurgitation is leakage of blood backward through the heart’s mitral valve each time the left ventricle contracts. It can result in congestion around the heart and lungs, atrial fibrillation (a condition in which the atrium pumps rapidly and erratically), and even heart failure.
Traditional surgery to repair or replace a mitral valve requires opening the sternum, Ferrari explains. Knight, however, prefers a less invasive approach through the side of the chest.
Even with this latter approach, however, a key challenge remains. “With the patient on coronary bypass, there’s essentially no blood in the heart,” Ferrari explains. “The atria deflates and falls on top of the mitral valve.”
So even adopting Knight’s approach, a second opening has to be made in the chest wall to insert a plate that helps hold the atria up so surgeons can see the mitral valve. And this, too, has its shortcomings. The plates often have to be adjusted throughout the surgery.
The team’s solution avoids the need for that second opening. They have come up with a device that can be inserted through the opening in the side of the chest, then deployed in a way that holds the atrium up, giving surgeons a better look at the mitral valve. It also allows them to work through the middle of the device.
“It’s a very small space,” Meyers says. “There’s a lot going on. They’re working with tools already six to eight inches long in the middle of the person’s chest, so we have a lot of environmental factors that play a role here.”
“This is what excites us to be medical engineers,” he adds. “To get to learn this crazy cardiovascular plumbing system, and take into account a lot of mechanical aspects as well.
“It is really exciting stuff.”
(The device that the team developed is now being reviewed by UR Ventures, the University’s tech transfer office, which is considering whether to apply for a patent.)
‘Doing it is a lot different than learning it’
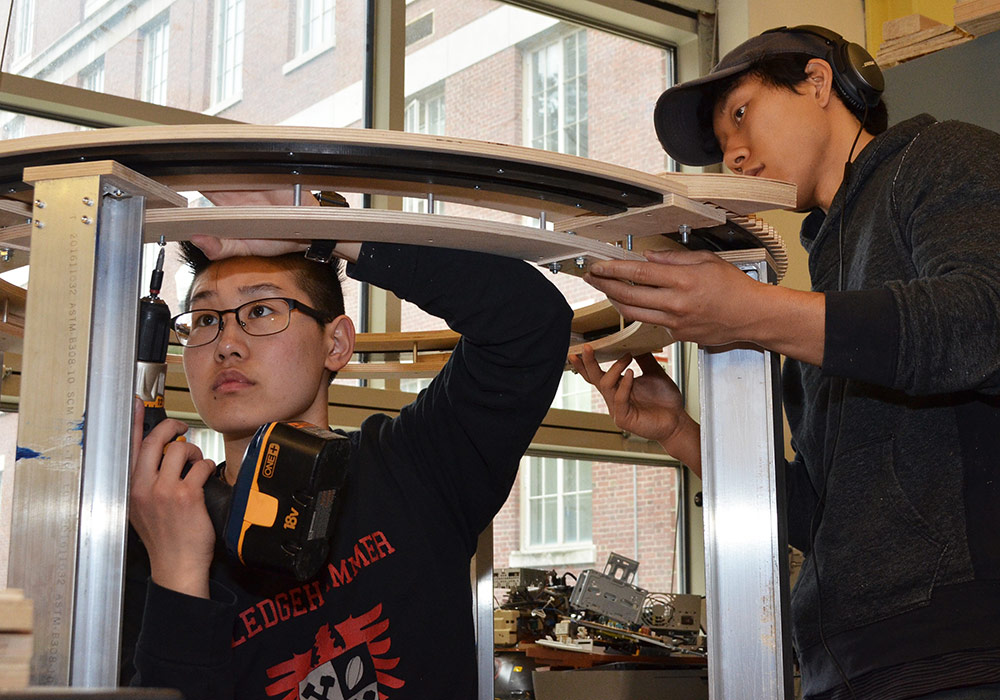
“Ideas for senior design sometimes come out of the blue,” says Professor Wayne Knox, who supervises the projects at the Institute of Optics.
That was certainly the case when David Krinick ’11, a community artist in New Rochelle, New York, contacted Knox last summer about erecting a 70-foot-tall, submarine-like periscope in the town’s square.
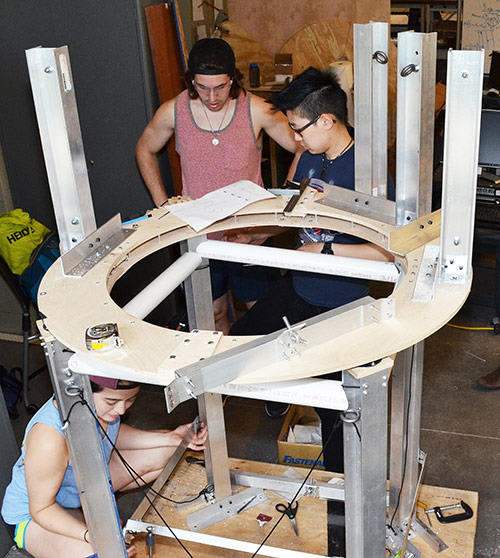
Krinick, the founder Mesh Print Studio, wants everyone in his community—not just those fortunate enough to live in the upper lofts of the town’s largest buildings—to enjoy a view of Long Island Sound, 1.2 miles away. He also specified that the periscope should be completely analogue—no electronics, no motorization.
Just lenses and mirrors.
As is often the case with unusual requests like this from nonengineers, Knox considered this from four angles. “At first you think ‘that sounds cool’ . . . then ‘no, that’s ridiculous’ . . . to ‘it might be possible’ . . . and finally ‘this could actually have educational benefit.’”
Chris Muir, who teaches senior design in the Department of Mechanical Engineering, concurred.
As a result, teams of students from each department have been working in tandem to demonstrate how the New Rochelle periscope really could be built.
The optics team of Jessica Bernstein, Yvonne Bodell, and Katherine Smith started by doing a patent search through existing periscope optical designs.
Then they came across something intriguing. “We randomly found it online one day,” Smith says. A shipping container—like the ones that can be used interchangeably to haul cargo on ships, trains and trucks—was set on its end in South America. It was adapted to house two large mirrors.
The team concluded a similar approach could be applied in New Rochelle. Two highly reflective mirrors could be vertically positioned 70 feet apart, at 45 degrees respective to each other, “allowing the image collected by the top mirror to project onto a second mirror at ground level that many people would be able to see.”
But how would it be housed?
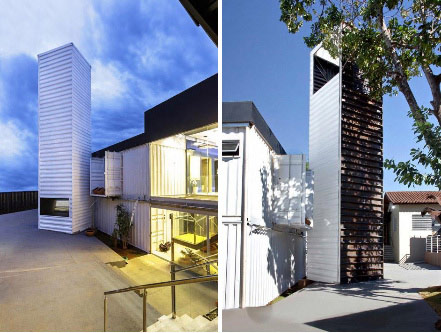
The mechanical engineering team of Hiroyuki Asaga, Carolyn John, Michael Kaplan, and Catherine Yip, have answered that question with a design that accommodates two mirrors up to six feet across, plus mountings for the mirrors and mechanisms for rotating and tilting them.
The team is now fabricating a seven-foot prototype to display on Design Day. It’s not exactly to scale. The mirrors are three feet across rather than only six inches in diameter—“which wouldn’t provide an accurate depiction of what we’re trying to accomplish, with the mechanisms we’re using to rotate the periscope and adjust the mirrors,” John says.
In the meantime, the optics team has come up with two other options. One replaces the bottom mirror with a telescope, to allow magnification. The other would look much more like the typical submarine periscope seen in the movies. It would consist of a relay system of small, five-inch lenses placed inside a 70-foot-tall PVC pipe.
“Originally we thought [this option] would never work; our professors thought it would never work,” Smith says. Why? Lenses bend light as it passes through them. Too many lenses, it was thought, would be needed to keep bending and re-bending the light to keep it focused along a 70-foot length.
“We got it down to eight lenses, with an objective at the top and an eyepiece at the bottom,” Smith says.
And their simulations say it should work.
It’s not clear whether the New Rochelle periscope will ever be built. But the project has served an important purpose. It gave the students a challenging problem to apply what they’ve learned in the classroom. “All of the classes we’ve taken were useful,” Smith says.
But it also opened their eyes to things that can’t be learned in a classroom.
“None of us had experience with a structure this large, or one using optics,” says John of the mechanical engineering team. “So we had to figure it out as we went.”
“I don’t think we realized how much time it would take for the full design to come together,” Yip adds. “I think we have a better idea of that now.”
In other words, “Doing it is a lot different than learning it,” Smith says.
Knox is especially pleased that teams from two different engineering disciplines were able to work in parallel on different aspects of the same project. He would like to see happen more often. After all, that’s what engineers do in the real world.
“This is a perfect example of really needing to do interdisciplinary senior design.”
A better way to extract the objects that don’t belong in a dog’s stomach
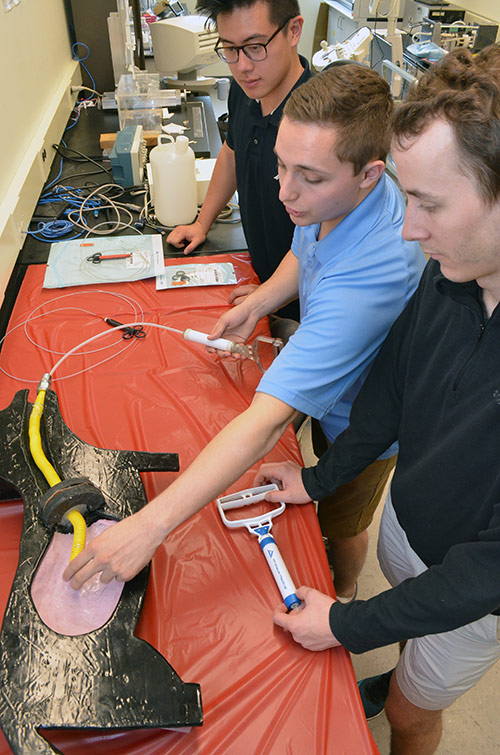
There is a widespread misconception that most pets can easily “pass” the objects they swallow.
Erika De Papp knows better. A veterinarian with the Massachusetts Society for the Prevention of Cruelty to Animals–Angell Animal Medical Center, she often struggles to extract objects lodged in a pet’s stomach or esophagus.
So when she heard about the Department of Biomedical Engineering senior design program from her nephew, a student in the department, she proposed a project: Build me a better device than what’s on the market now to extract these objects.
Seniors Connor McBride, Edward Ruppel, and Chandler Woo believe they’ve done exactly that.
“Her pitch to us was that one of the common issues with current devices is that it is very difficult to grasp an object in an animal’s stomach,” Woo says. “Some procedures last up to an hour and a half, and when it gets too frustrating, they resort to surgery. Obviously it would be better to be less invasive.”
The team designed a small plastic tube that can be inserted down the esophagus and into the stomach. Inside the tube is a wire that can be extended out the end of the tube, deploying into a cage-like head that fits around the object. When inserted in the biopsy port of an endoscope with a camera in its tip, it allows one member of the veterinary team to keep the object in view, while the other secures the object.
“We’ve focused this design on 40 to 60 pound dogs, but could easily adjust the length to work with humans, chimpanzees, giraffes—whatever you want,” says Ruppel.
Devices already on the market may seem similar, but they are limited to sliding the wire forward and back (a single “degree of freedom”). They require the veterinarian to choose from myriad head shapes, which often deform and have to be discarded.
The team’s device, now in its third iteration, is more robust. It incorporates two additional degrees of freedom—rotation and translation—“for additional precision” in maneuvering the head to grasp the object, McBride explains.
For example, the wire head can be rotated, which is crucial to realigning a shard of bone so it does not tear the stomach or esophagus as it is pulled out, Woo says. The tube itself can be bent, or translated.
And the device can be locked in place at any point during the procedure, which makes it easier for the other member of the team to lend a hand during the extraction, Ruppel says.
Those additional degrees of freedom exceeded the team’s initial assessment of what they needed to do to meet their client’s needs. “We wanted to take the design further,” Woo says.
The components, designed in Solidworks, can be fabricated with injection molding. “This puts us in position to easily commercialize if given the opportunity,” Ruppel says. The team is working with UR Ventures, the University’s tech transfer office, to assess the possibility of a patent.
The biggest challenge for the team: the narrow tolerances of the design. “We were working with 2 millimeter tubing, which is really small. We had to be sure when we ordered wire (custom-made) that it would fit inside,” McBride says.
The other challenge was staying within budget. The teams are allotted $150 per member. “It’s actually good to know we’re within a limited budget,” Woo says. “That’s something we have to learn for the work we’ll be doing in the future.”
It helped that Ruppel was familiar with the 3-D printing and other resources at the fabrication lab at Rettner Hall, which helped keep down costs. Ruppel is president of the Solar Splash team, which builds a solar- powered boat for intercollegiate competition.
All three members of the team will pursue graduate degrees in medical device development. Ruppel will be in the master’s degree program at the Center for Bioengineering Innovation and Design at Johns Hopkins. McBride will remain at Rochester with the Center for Medical Technology and Innovation master’s degree program in medical device design. And Woo will attend Rice University, pursuing a master’s degree in its global medical innovation track, which trains students to develop low-cost solutions for emerging countries.
“That was one of the cool things about this project,” Woo says. “This is the sort of path we all want to pursue.”
A design project that will endure
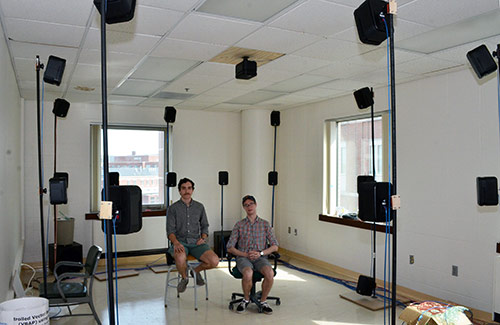
Imagine immersing listeners in sounds that you’ve splashed all around a room—much as an artist might splash paint on a canvas.
Future students in the audio and music engineering program — offered by the Department of Electrical and Computer Engineering — will be able to do that, thanks to the capstone project of seniors Tim Dick, Matt Dylewsky, and Frank White.
With financial backing from the department, they’ve strategically placed 29 speakers on stands all along the walls of a room in the Computer Studies Building, creating a cutting-edge surround-sound studio.
The software program they’re using is MAX MSP, advertised as the “ultimate sonic toolkit.” It enables one set of speakers, for example, to project the sound of a truck roaring by on your left, while another projects the conversation of pedestrians on your right.
Vector based amplitude panning allows each speaker to be sequenced and weighted for maximum effect, so that sounds come at you from set directions one moment, then literally swirl around the room the next.
“We wanted to make a high-density, surround-sound environment that students majoring in audio and music engineering could use to mix their own projects in current surround-sound formats,” White says. “But we wanted it to also be extensible to formats that don’t currently exist, and also to some interesting sound field recording techniques.”
For example, Dylewsky holds up a department-owned ambisonic microphone, showing how the four sound-gathering capsules are angled orthogonally away from each other to gather sounds of equal quality from multiple directions.
The team recently used the microphone to record a performance of the University of Rochester Brass Choir in Strong Auditorium. Director Bill Tiberio positioned the musicians all around the edges of the stage, and even in the balconies, so they surrounded the audience.
When White plays the recording, the sound of brass instruments fills the room from all directions, like a warm sonic blanket.
The studio will be an important instructional resource for the department’s audio and music engineering major. The program prepares students for a range of careers in sound engineering—for example, creating music for video games or immersive sound effects for virtual reality.
White says the team would also like to get some “crosstalk” going with Eastman School faculty and students about the studio’s potential use for music composition, using a joystick–based compositional tool.
“Imagine going into the room with the music you’ve created, and having a joystick to pan the sound around the room, and be able to hear exactly where it’s going based on what you’re doing with the joystick,” White says.
The idea for the project originated with department chair Mark Bocko, who originally envisioned a “geodesic dome”–like array that would ensure each speaker was perfectly equidistant from a listener standing at the center. However, an array large enough accommodate larger groups of people would have taken too much space.
So part of the challenge for the team was to develop an alternate design that would come closest to matching a spherical array. They’ll continue to make refinements the rest of this semester, then put everything they’ve learned and done into a manual so future students can keep adding on.
Many senior design prototypes, once completed, are dispensed with, having fulfilled their purpose simply in the making. Not this one. “This crazy space we’ve built will exist somewhere in this building in perpetuity,” White says.
A color-tracking Hexacopter
These days, it has become more routine to look up in the sky and see small drone flying overhead. The uses for these unmanned aerial vehicles are becoming more numerous by the day, but the technology put into them hasn’t been fully explored.
Electrical and computer engineering students Alexander Alling, Yizhe Cheng, Philip Fenimore, Joseph Lasekan and Hongji Yang wondered if it would be possible to add more computing power to the drone, and make it a little smarter in the process.
Starting from scratch, the team built a hexacopter capable of carrying the hardware they wanted to mount on it. Their goal was to program the drone to automatically locate objects based upon color and then track the object.
To do this, they had mount a camera, sensors of various types to calculate distance and speed, as well as a computer capable of running an algorithm that would handle the job of identifying color information and then tracking it.
The result is quite a complex piece of machinery, and while it might not yet have a specific application, the understanding could help to develop other advanced capabilities and program them into these aerial vehicles to enhance the ways that they can be used.