Equipment
Wire Bonder
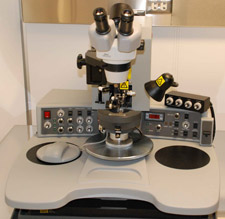
Model:
K&S Wire Bonder
Capabilities:
This tool is capable of bonding small wires to contact pads using a combination of ultrasonics and heating.
Cost:
Calendar for Reservations:
Specifications:
- Al wire.
- ball and wedge bonding capable.
Wire bonding is the method of making interconnections between an integrated circuit (IC) or other semiconductor device and its packaging during semiconductor device fabrication. Although less common, wire bonding can be used to connect an IC to other electronics or to connect from one PCB to another. Wire bonding is generally considered the most cost-effective and flexible interconnect technology, and is used to assemble the vast majority of semiconductor packages. A person upon first seeing a ball bonder will usually compare its operation to that of a sewing machine. In fact there is a needle-like disposable tool called the capillary, through which the wire is fed. A high-voltage electric charge is applied to the wire. This melts the wire at the tip of the capillary. The tip of the wire forms into a ball because of the surface tension of the molten metal.
The ball quickly solidifies, and the capillary is lowered to the surface of the chip, which is typically heated to at least 125°C. The machine then pushes down on the capillary and applies ultrasonic energy with an attached transducer. The combined heat, pressure, and ultrasonic energy create a weld between the copper or gold ball and the surface of the chip - which is usually copper or aluminum. All aluminum systems in semiconductor fabrication eliminate the "purple plague" (brittle gold-aluminum intermetallic compound) sometimes associated with pure gold bonding wire. This property makes Aluminium ideal for ultrasonic bonding. This is the so-called ball bond that gives the process its name.Next the wire is passed out through the capillary and the machine moves over a few millimeters to the location that the chip needs to be wired up to (usually called the leadframe). The machine again descends to the surface, this time without making a ball so that the wire is crushed between the leadframe and the tip of the capillary. This time the surface is usually gold, palladium, or silver - but the weld is made in the same way. The resulting weld is quite different in appearance from the ball bond, and is referred to as the wedge bond, tail bond, or simply as the second bond. In the final step the machine pays out a small length of wire and tears the wire from the surface using a set of clamps. This leaves a small tail of wire hanging from the end of the capillary. The cycle then starts again with the high-voltage electric charge being applied to this tail.